A simple article takes you to understand the detailed practical operation and common problems of water transfer printing production process.
1. Topcoat: according to the material of the workpiece to be transferred, carry out decontamination, deoiling, antirust treatment, and remove residue or flame;
2. Drying treatment: according to the characteristics of the topcoat, select the suitable temperature to carry out drying treatment for the topcoat;
3. Film selection: select the texture of pre transfer printing or customize according to the plan given by customers;
4. Film placement: the film paper with the size of the workpiece to be transferred is paved on the river (the packaging and printing face down);
5. Activity: when the membrane paper is still on the river for 60-90 seconds, spray the active agent evenly on the membrane paper. The water transfer plastic film is spread on the surface of the transfer stainless steel flume, with the graphic layer facing up, to keep the water in the stainless steel flume clean, and basically neutral. The active agent is used to spray paint evenly on the surface of the picture and text to make the picture and text layer active and easy to separate from the media plastic film. The active agent is an organic chemical mixed organic solvent dominated by aliphatic hydrocarbon. It can quickly melt and destroy acrylic emulsion, but it is not easy to destroy the image and text layer.
Operation and problems in water transfer process
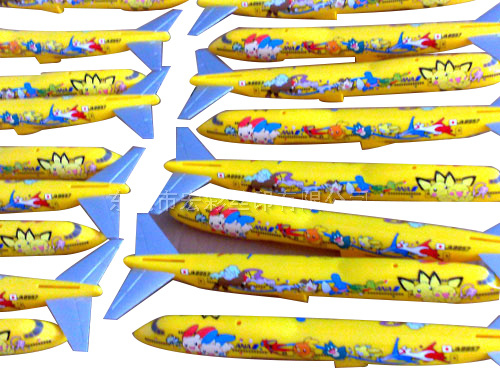
6. Transfer printing: 5-10 seconds after spraying the active agent, keep the workpiece with migration product at 35 degrees to the membrane paper, from top to bottom, with uniform diastolic pressure. When the objects that must be water transferred are slowly approached to the water transferred plastic film along its corridor, the graphic layer will gradually migrate to the commodity surface under the effect of pressure, because of the original adhesion effect between the printing ink layer and the printing process raw materials or unique coating. In the whole process of transfer printing, the matching speed between the printing process and the water coating should be kept symmetrical to prevent the plastic film from wrinkle and make the picture and text not good-looking. Under normal circumstances, we should ensure that the graphics and texts are properly drawn, and try our best to reduce overlap, especially at the junction. If there are too many overlaps, it will give people a sense of disorder. The more complex the commodity is, the higher the requirement of practical operation is.
7. Soaking: soaking water transfer products for about 30 seconds, so that the printing ink can adhere to the products more smoothly;
8. Cleaning: remove the product workpiece from the stainless steel sink, remove the residual plastic film, and then wash the floating layer without contact inhibition on the commodity surface with cold water. Pay attention to the pressure can not be very big, otherwise it is very easy to transfer the text caused damage.
9. Drying treatment: remove the moisture on the surface of the goods, in order to facilitate the transfer printing ink completely dry, improve the adhesion color fastness, you can use the hair dryer dry, you can also put the goods in the oven dry. The drying temperature of plastic products should not be too high, about 50 ~ 60 ℃. Too high temperature is very easy to deform the printing process; The drying temperature of metal materials, laminated glass, porcelain and other raw materials can be moderately increased.
10. Paint solution: in order to improve the resistance of the graphic layer to the natural environment, it is necessary to carry out spraying on the surface. Spray can use solution type varnish, spray after the course of dry or heating dry; Can also use UV varnish, choose UV dry solid dry. In comparison, UV curing is more integrated into environmental protection regulations. Solution based varnish should be mixed with the sealing curing agent of supporting facilities. For example, the water transfer paint varnish produced by a certain manufacturer is a varnish with polyurethane adhesive as the interconnection material, which should be used with PU sealing curing agent; The thickness of the coating can be controlled by adding appropriate paint thinner to improve the viscosity of varnish; Be careful not to dry in the oven. For different printing process raw materials, spray varnish is also divided into three types, namely suitable for plastic materials varnish, suitable for soft raw materials varnish and suitable for metal materials, laminated glass